Since we base our production on a program for making vases and lanterns which are made from the highest quality aluminum alloy,we paid the greatest attention exactly the procurement of basic raw material because it is the foundation of all stages of our production process.
Supply is made of suppliers with whom we have a long tradition of business and that for several decades engaged in the production of aluminum alloys.
Our production program is consist in making ten models, and in our the basic program they are made in two colors: dark gray and gold, but we can make them in other colors and shades in prder of customer (eg. Black, silver, etc.)
Supply is made of suppliers with whom we have a long tradition of business and that for several decades engaged in the production of aluminum alloys.
Our production program is consist in making ten models, and in our the basic program they are made in two colors: dark gray and gold, but we can make them in other colors and shades in prder of customer (eg. Black, silver, etc.)
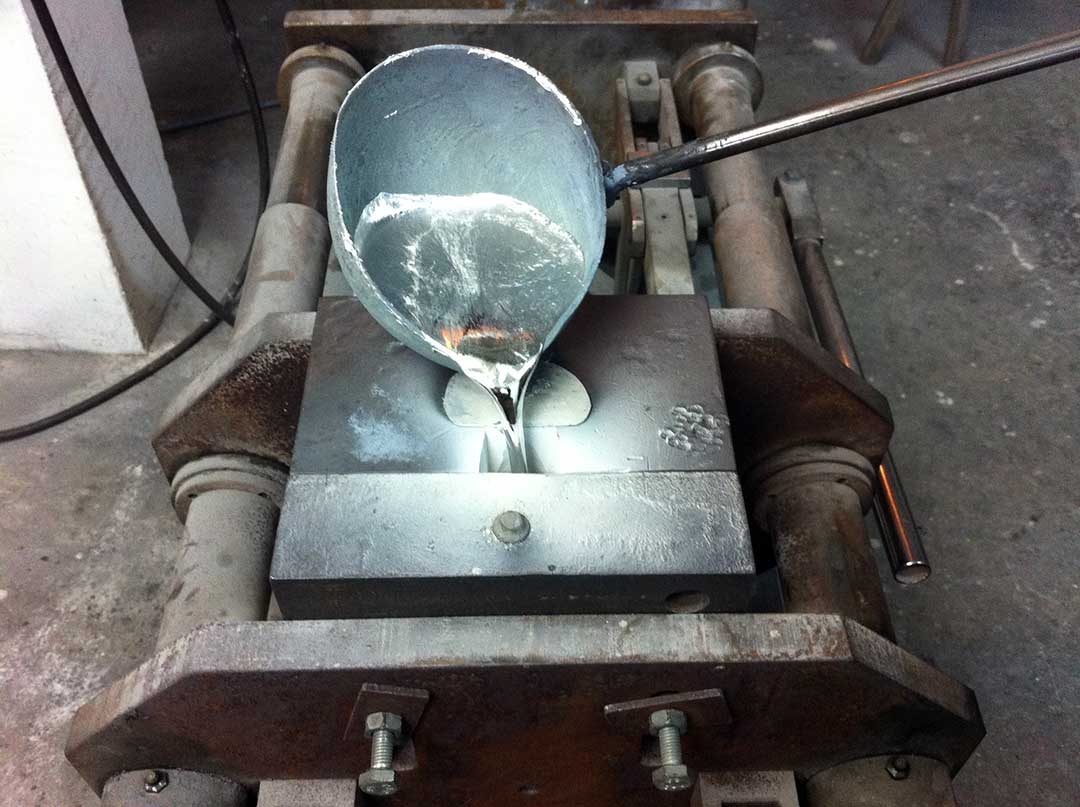
The next stage of the production process is the opening of the permanent mold and demolding. In order to successfully separated drip-moulding from mold, first it has to be cooled by compressed air, and then expose to a brief heat. If all the parameters and conditions in the preparation of casting are met, then we achieved relatively high amounts of castings per each cycle.
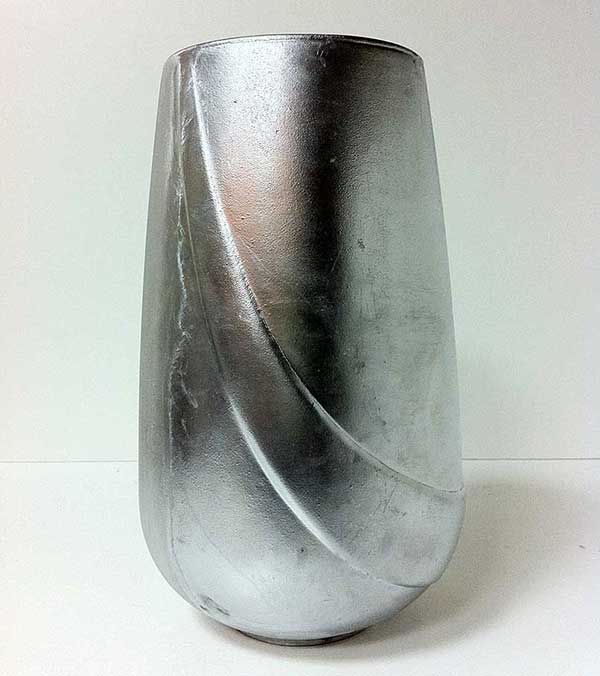
All funerary vases and lanterns are protected by high-quality clearcoats. Applying the finishing layers of varnish takes place in a specially prepared chamber. All other necessary materials used in the production, as well as our products in various stages of production, subject to constant control.
The production is organized in several stages using different technologies of production:
– Gravity casting in ingot
– Machine or hand casting
– welding
– Surface treatment and protection with colors
– varnishing
– Packaging and storage
– Gravity casting in ingot
– Machine or hand casting
– welding
– Surface treatment and protection with colors
– varnishing
– Packaging and storage
The first phase of production covers the casting of molten aluminum into molds. Technical terms for this procedure is, so called., chill or gravity die casting, which means the process of casting in metal molds or mold where the aluminum alloy flows by force of gravity. In this procedure mold cavity fills with alloy which gradually solidifies and forms the desired molded part. Casting in the ingot is achieved relatively high accuracy of casting,so their mechanical treatment is reduced to a minimum. That is how we reduces the cost of material, energy and time. Such technology is considered to be in today’s competitive and modern.

After demolding from mold we approach to its mechanical and manual processing. At this stage, we remove excess material by circular blade. After that drip-moulding is handled by pressuse grinders so that later, in hand-stage processing, less material has to be removed. Once completed machine or hand treatment, castings are ready for welding. The following procedure is a method of surface treatment (sandblasting) and protection with colors, and as the last step is painting vases or lanterns.
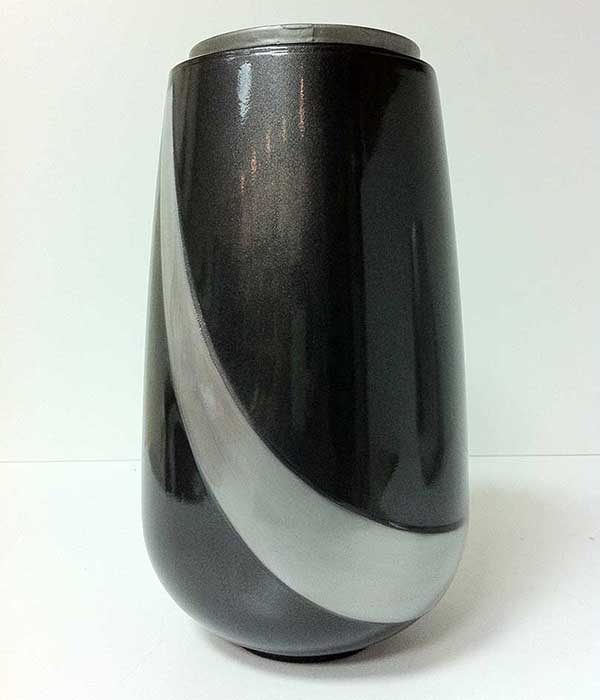